I’ve already discussed this at length on my youtube channel so this is more or less a transcription for those of you out there who can’t stand the sound of my voice. I’m sure everyone is just excited to see me finally posting about an engineering project.
About a month ago, I watched a bunch of Spider-Man movies back to back. The natural conclusion from this was that I too wanted to climb walls. It seemed like a good combination of engineering challenge and self-endangerment so I began doing research.
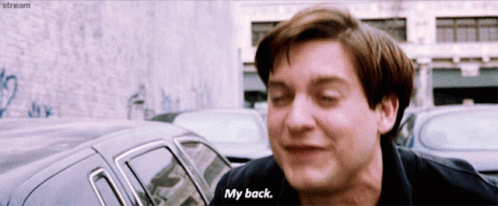
I came across a fairly old concept that I first saw in the form of this competition done by the air force in 2012 where they challenged different universities to create a system that let someone reach the top of a 90 foot concrete silo. The winning design by students at Utah State University used dual back-mounted vacuum cleaners with hoses running to large pads in each hand that acted as a sort of powered suction cup.
Suction cups have been used to climb all sorts of things in the past, but they are usually only good for extremely smooth surfaces like glass. Powered suction cups like this work the same way except they have some sort of fan or pump actively pulling the air out of them. These require much less perfect conditions to get a good seal and you can see them used on an industrial scale for moving things like paving stones.
The students from Utah State built their version of this using battery-powered vacuum cleaner motors which are pretty good because they can move a lot of air quickly, but they are very large and I wanted to build a device that was entirely self-contained. I also wanted to do it without spending $20,000 and 9 months of development time.
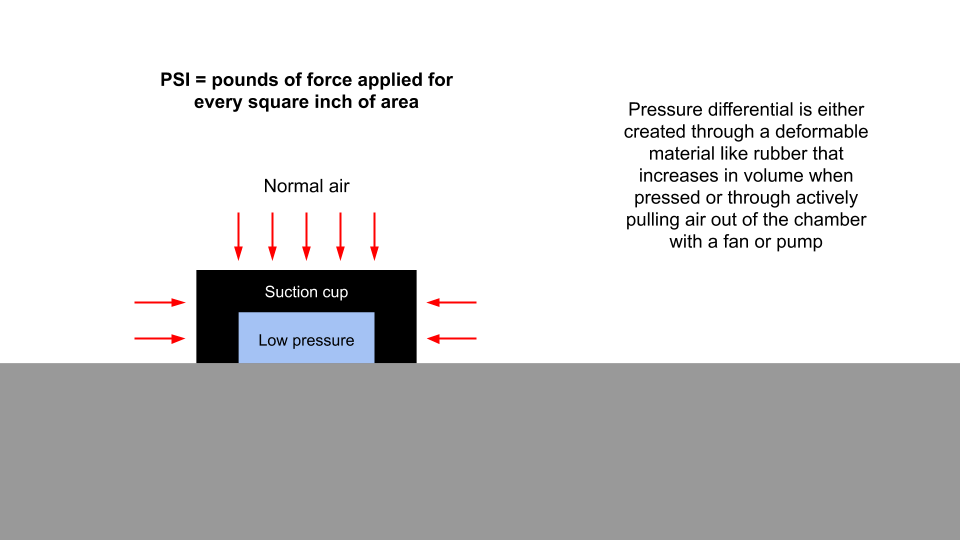
Suction cups work by creating a pocket of vacuum, or as close as you can get, between your device and the surface. The outside air will then push on your device with a force directly proportional to the surface area of that vacuum pocket.
My initial thought process was vacuum cleaner motors because this is what everyone else had done, but since I wanted the devices to be self-contained I needed to find something smaller. The first thing I tried was ordering a blower motor for a roomba-like product off of ebay. I was skeptical that this would be able to provide the pressure differential that I wanted but I began some preliminary plans anyway while I waited for it to arrive.
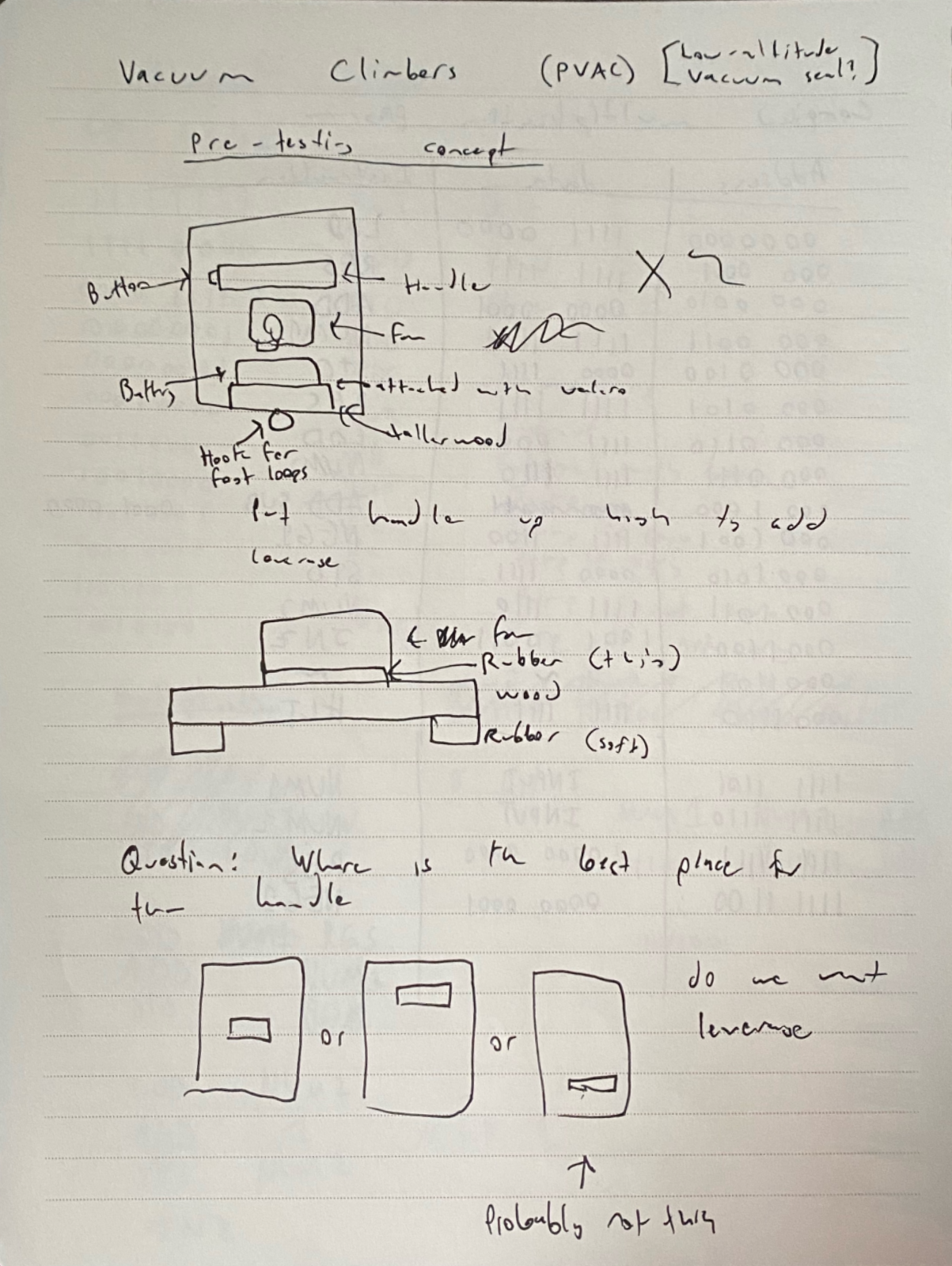
I wanted to keep the size of the pads down but I knew that if the motor was less powerful than I was hoping for then I could just make them a little bit bigger for the same effect. My goal was for each hand to be able to hold around 400 pounds perpendicular to the surface they’re attached to.
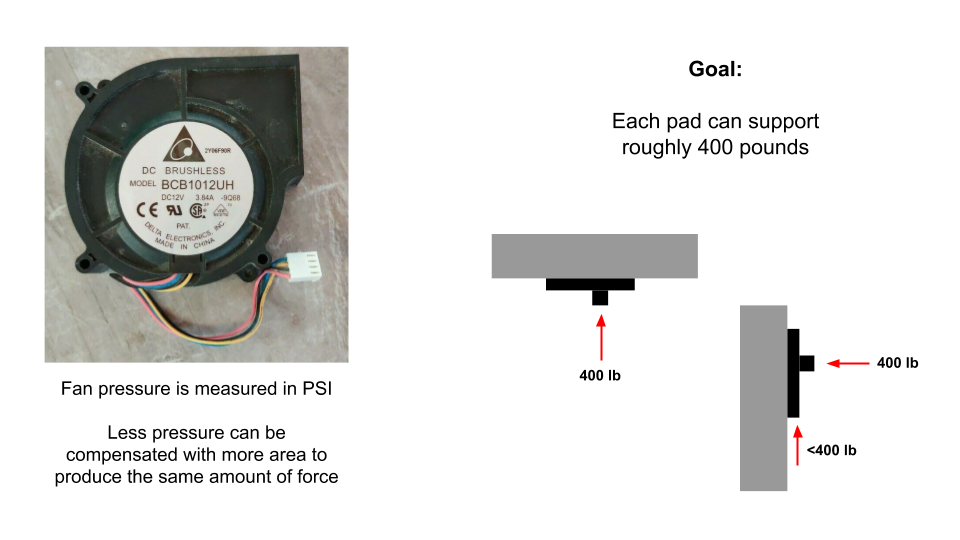
The vacuum motor arrived and I was very underwhelmed with the result. My basic test where I measured how many inches upward it could suck water in a tube showed that the motor could only produce about 0.4 psi of vacuum pressure. That means that to lift 400 pounds I’d need pads with 1000 square inches of surface area.
The roomba motor was a dud but luckily it only cost like $8. I needed something new. I went back to ebay and started looking at vacuum pumps. I found these DC diaphragm pumps for around $15 and I ordered two.
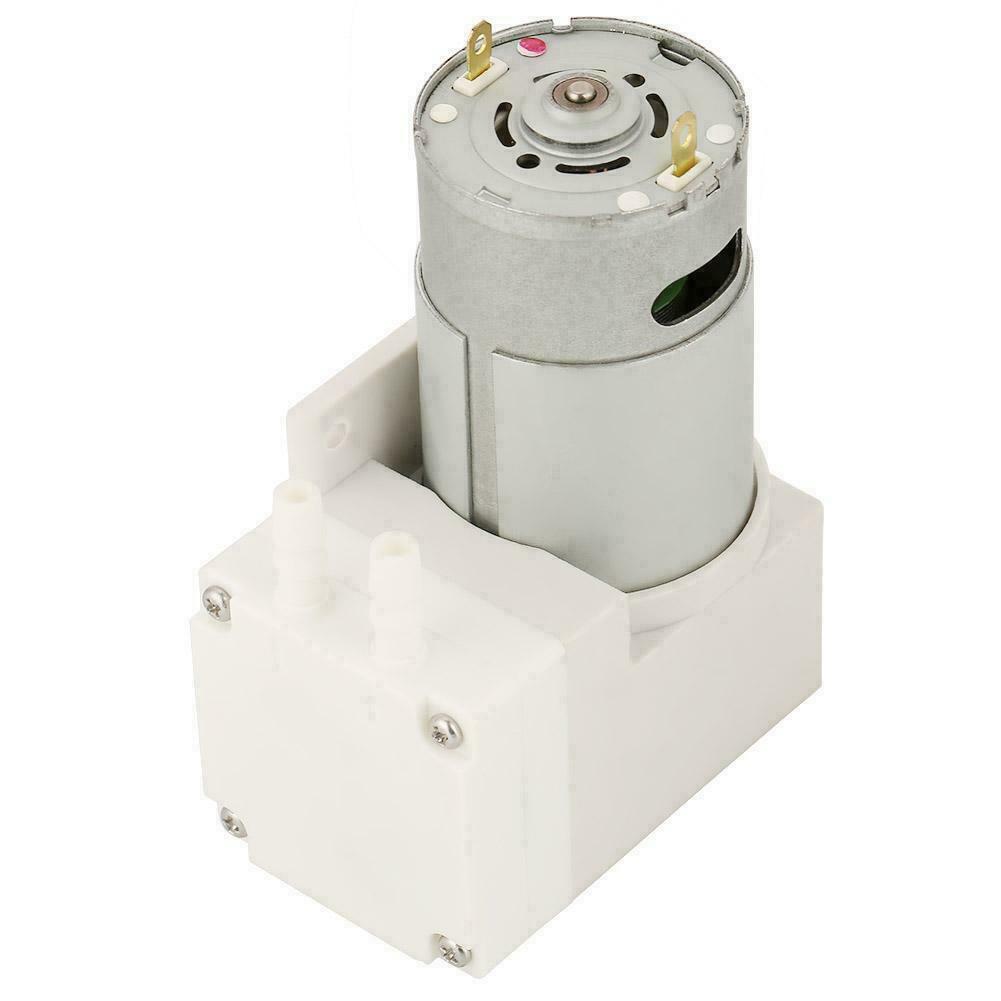
Generally speaking, a pump moves air much less quickly than a fan, so it wouldn’t make sense for an application like a vacuum cleaner, but they can also allow you to reach much higher pressures. This pump was advertised as being able to reach -76 kilopascals which is about 11 psi.
I revised my design and settled on a device size of 1 square foot per hand with a vacuum area of 11 by 12 inches. With a perfect 11 psi this would net me 1452 pounds of suction with each hand, although I’m sure the result is considerably lower than that.
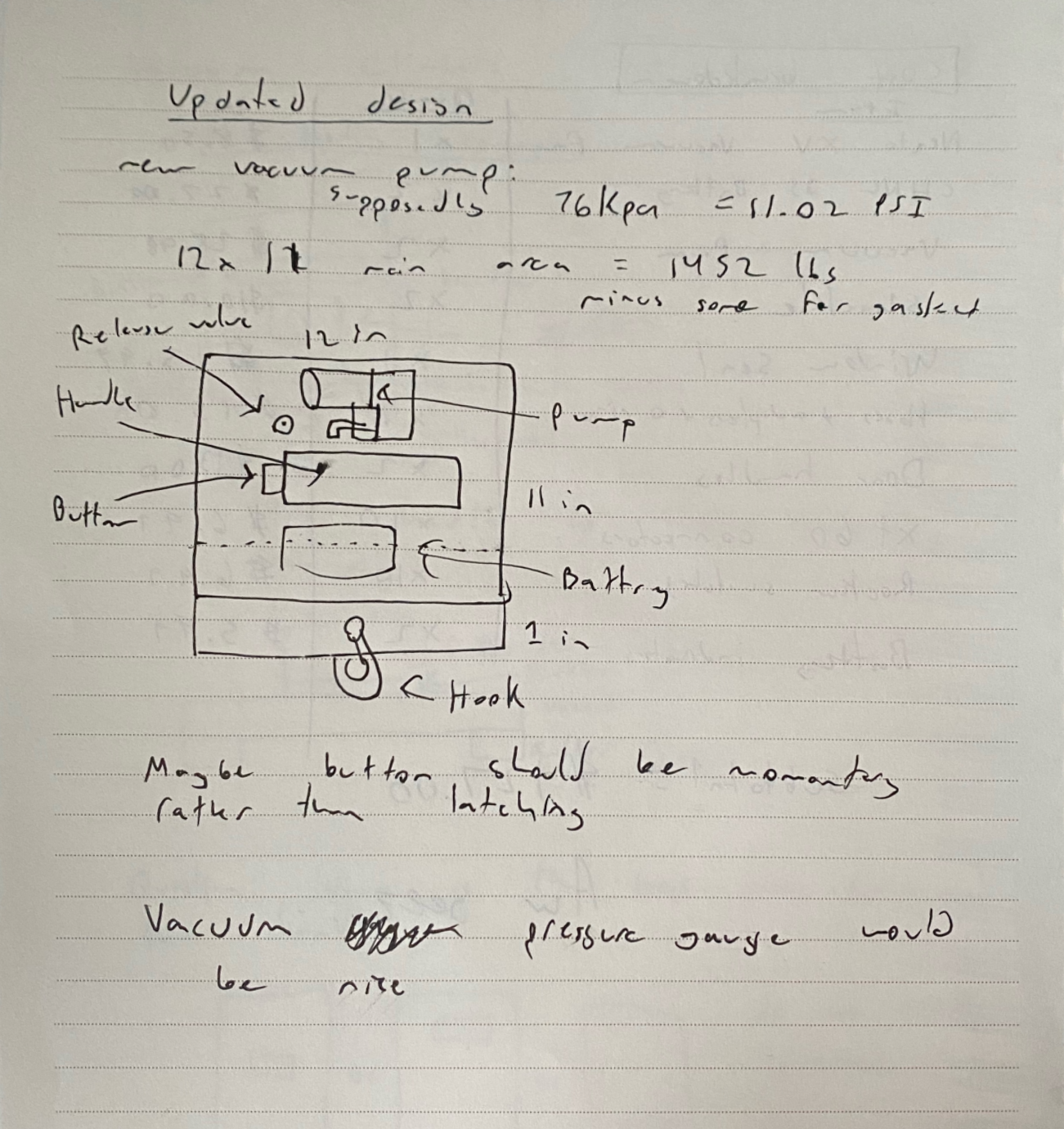
From here, the rest was simple. I made the two pads out of cheap plywood and I powered the pumps off of 12v 2200mah lithium ion batteries which would give me about a half hour of suction time based on the pump’s rated 50 watt power consumption. I bought door handles made out of bent steel tubing for the user to hold onto and I added on off switches and battery indicators to each device.
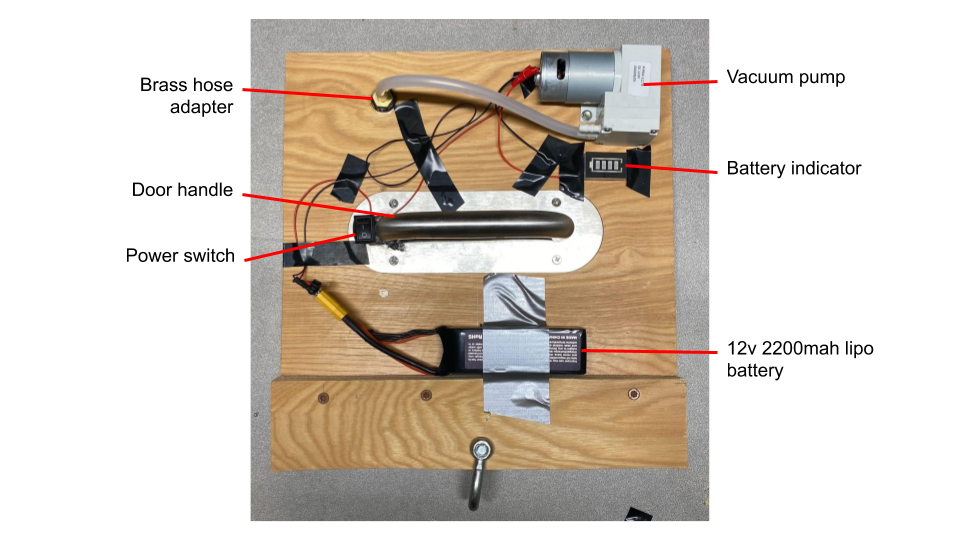
One of the most important considerations was the gasket that would form the seal between the wood and the wall. This needed to be something soft so that it could form a tight seal and make it into any small deformities in the material. It also needed to be something grippy so the pads wouldn’t just slide down the walls when you put any weight on them. To accomplish all of this I settled on some silicone weather sealing strip meant for windows and doors.
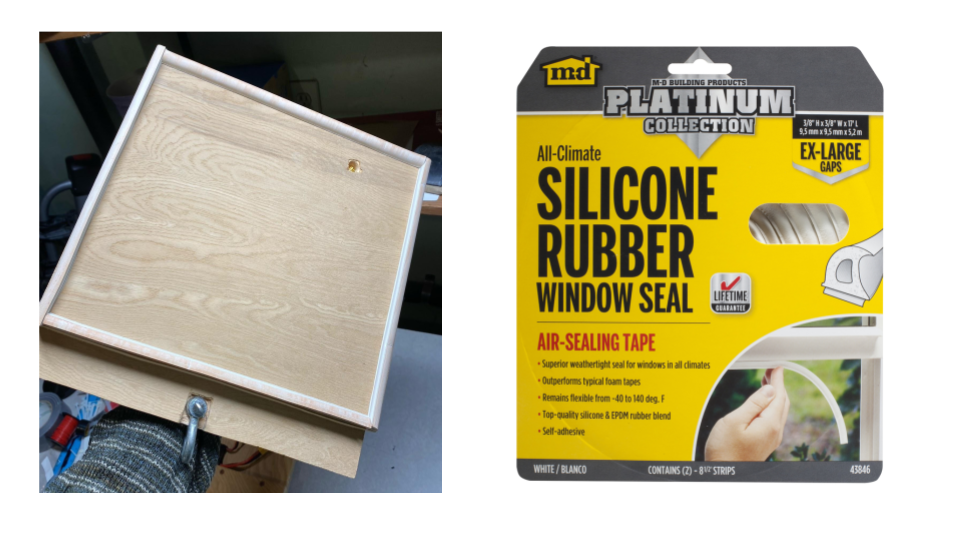
Another important consideration was how much energy the user would have to put in. Now I obviously could do pull ups all day, but for those out there that don’t want to do that I decided to add optional foot straps. These were just some loops of rope that I put a little pvc pipe on that attached to the bottom of each climber. This way, all the weight could be transferred to your feet, taking away almost all of the physicality out of the climbing.
The devices are actually incredibly simple, but I still ended up spending like $100 total to make them because of all the stuff I had to buy in bulk. If I was to build another pad it would probably only cost around $35.
Okay, so the first test didn’t go great. But I learned that to get a good seal you have to initially give the climber a good push so that the gasket can expand and fill all the cracks. I took what I learned and performed several more successful tests.
Despite my initial failure, I felt confident to give the climbers their first real-world test. I found this large concrete wall and began my climb. I ended up going all the way up and down about 15 feet twice. The devices worked remarkably well and I learned a lot.
I found that an alternative to pushing the pads firmly against the wall to get a good seal, you could also slide them down the wall a bit until they locked themselves in place. I also found that I was able to go down without lifting the pads from the wall at all. I just had to disengage the pumps, slide them down the wall, and re-engage. I think with enough practice I could do a similar technique while climbing up which would make things even quicker.
My test went better than I could have hoped for, but there were also some obvious problems. One that I did not anticipate was a design flaw with the foot straps. When I made them I didn’t put much thought into it but I figured that adding the bit of pipe would help the rope to not squeeze your foot so hard. That worked but what also happened was that the straps slipped off your feet very easily. Because their design was totally flat, they would then press up against the wall and become very difficult to slip your foot back into.
Most of the jankiness of the climb was from me trying to maneuver my feet back into straps, but if this is the largest problem I’m totally okay with that. The other component that needs the biggest improvement is the gasket. While it does form a pretty good seal on completely smooth surfaces, it’s not thick enough or soft enough to climb rougher surfaces. I can stick to wood, glass, concrete, and metal as long as it’s smooth but I can't climb something like brick. It also has the problem of forming a good seal in the corners. I made the pads a square to maximize surface area, but it also means I had to make the gasket out of separate strips which don’t form a perfect seal until they’re compressed.
Perhaps most importantly is the massive element of danger to it all. I have an irrational amount of trust in things that I’ve made myself, but I have to acknowledge that hanging from door handles screwed into cheap plywood is a recipe for injury. I felt very safe going 15 feet up, especially because I had two hands attached at almost all times, but I would be pretty scared to go much higher with the devices in their current form. The nice thing is that all of these problems are fixable or at least manageable. The foot straps need an immediate redesign to something more 3D so they can be easier to slip into.
My goal is to eventually be able to climb brick so I’d like to make the gasket out of a different product altogether, maybe even cutting it out of one large sheet, but if I can’t do that I will have to consider making the pads a circle so that I can use one continuous strip. While I don’t think I got the 1400 pounds that were possible with the pumps I used, I think I got at the very least 400. I could probably manage to make them circles without increasing their size and still be able to support plenty of weight.
Of course the plywood will have to go soon for something more durable that can house all the components in a much more contained fashion. I’d also love to add a pressure gauge to the climbers so that you can see how good of a seal you have before you put any weight onto them. If I did this and I was able to get a good enough seal, I could potentially not even need to leave the pump on to maintain the vacuum after sucking all the air out. This would also mean I’d need some sort of controlled release valve but it would let the devices be more power efficient and even quieter.
It’s incredibly satisfying when something you’ve been working on for a while finally comes together and I am blown away that this actually worked on the first try.